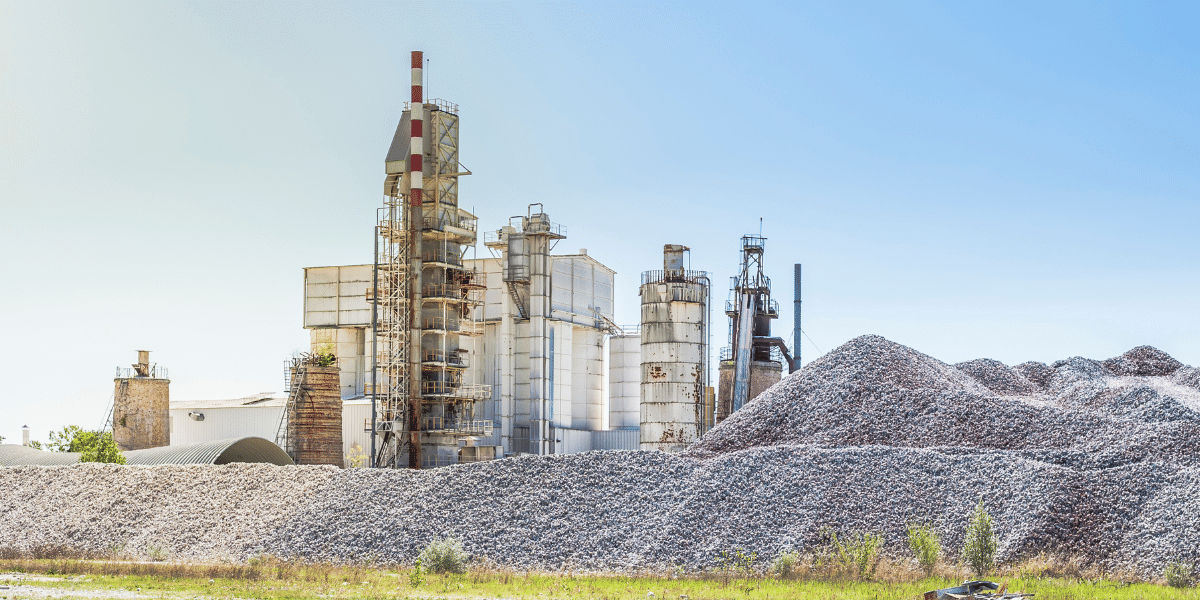
An essential strategy for reducing the global warming potential (GWP) of concrete relies on replacement of portland cement with supplementary cementitious materials or SCMs. Reducing high embodied carbon in portland cement with low-embodied carbon SCMs holds significant environmental benefits. On a global scale, SCMs have the potential to reduce CO2 emissions from cement production by over 350 million metric tons annually according to the Global Cement and Concrete Association.
In addition to reducing concrete’s carbon intensity, SCMs can increase strength, improve durability, reduce permeability, and lower costs. However, the challenges of replacing portland cement with SCMs include material availability, quality control, and construction efficiency. For the latter, fresh concrete workability through control of water demand without compromising strength and durability results in efficient placement and a long-lasting project.
Solidia Technologies is poised to address each of these challenges. This case study is about how Solidia’s engineered SCM delivers enhanced performance with reduced GWP. Together, they accelerate integration into cement manufacturing and concrete production.
Solidia Technologies met these challenges by designing an engineered SCM for partial replacement of portland cement in concrete. Solidia SCM (S-SCM) permanently captures CO₂ while offering enhanced concrete performance while serving as a viable replacement for fly ash. For decades, abundant fly ash, a coal by-product conforming to ASTM C618 and AASHTO M 295, improved concrete’s performance. Since 2010, however, fly ash supply and use have been steadily shrinking due to a diminishing number of coal-burning power plants. S-SCM addresses the declining fly ash supply and is a viable alternative to existing SCMs.
ASTM Committee C09 on Concrete and Aggregates is voting on a proposed Standard Specification for Supplementary Cementitious Material for Use in Concrete. When approved by ASTM, this performance specification enables use of alternative SCMs not governed by ASTM standard C618 for coal ash, C989 for slag, C1240 for silica fume, and C1866 for ground glass. S-SCM is anticipated to comply with this emerging ASTM SCM performance specification.
The emerging ASTM standard requires new SCMs to be evaluated according to ASTM C1709 Standard Guide for Evaluation of Alternative Supplementary Cementitious Materials for Use in Concrete. This guide includes SCM composition tests, and many concrete performance tests. The evaluation includes comprehensive laboratory testing and jobsite evaluations via full-scale field demonstrations. Extensive laboratory testing of Solidia’s SCM resulted in exceptional results. Full-scale demonstration projects in 2020 and more recently further increase designer and owner confidence.
In 2020, two concrete pavement installations in northeast Pennsylvania using S-SCM demonstrated performance under heavy truck traffic, winter climates, and deicers. The projects consisted of parking and driving areas at a cement manufacturing plant and a ready-mix concrete producer.
The mix design for both installations is shown below.
Air entrainer: 0.53 fl.oz/100 lb cementious Mid-range water reducer: 5 oz/100 lb cementitious
Installation completed July 2020
Traffic: Ready-mix concrete trucks
Concrete pavement volume: 10 cy
Water/cement ratio: 0.45
Slump: ~6 in.
Admixture: Air-entraining and mid-range water reducer
Test batch 28-day cylinder strength: 5400 psi (min. target 4500 psi)
Installation completed November 2020
Traffic: Cement trucks
Concrete pavement volume: 10 cy
Concrete pavement area: 12 ft x 20 ft x 11 in. thick reinforced concrete slab
Water/cement ratio: 0.45
Slump: ~6 in.
Test batch 14-day cylinder strength: 5300 psi (min. target 4500 psi)
*Now Holcim
Since 2020, S-SCM has been placed in industrial applications by multiple ready-mix concrete companies. While the above projects replaced 20% of the portland cement, additional engineering yielded exceptional performance at 35% replacement for 2023 and 2024 pours in industrial applications.
Contact us for additional information on the most recent generation of S-SCM. This includes excellent compressive and flexural strengths, plus beneficial freeze-thaw, sulfate, and ASR resistance.
S-SCM is made from Solidia Cement that meets ASTM C1905 Standard Specification for Cements that Require Carbonation Curing. In addition to 30% lower CO₂ emissions when compared to portland cement, Solidia’s SCM carbonation process permanently captures CO₂ up to 25% of the weight of processed Solidia cement in S-SCM via mineralization into calcium carbonate. CO₂ reductions achieved from Solidia Cement manufacturing, carbonation, and processing into S-SCM, plus portland cement replacement all contribute to reducing the GWP of concrete.
S-SCM carbonation can be through direct utilization of CO₂ in cement kiln flue gas or from other sources. The table below demonstrates possible CO2 reductions on portland cement and portland limestone cement replacement levels between 20% and 50% with 35% S-SCM replacement achieving optimum strength and durability requirements. S-SCM with reduced portland cement content can meet ASTM C595 specification for blended hydraulic cements or ASTM C1157 performance specification for hydraulic cement. additional engineering of S-SCM yielded exceptional performance at 35% and 40% replacement levels for 2023 and 2024 pours in industrial applications.
*GWPs from Portland Cement Association industry average EPDs **Does not include GWP for aggregrate, transportation, and ready-mix plant operations.
S-SCM is made from Solidia Cement® that meets ASTM C1905 Standard Specification for Cements that Require Carbonation Curing. In addition to 30% lower CO₂ emissions when compared to portland cement, Solidia’s SCM carbonation process permanently captures CO₂ up to 25% of the weight of processed Solidia Cement in S-SCM via mineralization into calcium carbonate. CO₂ reductions achieved from Solidia Cement manufacturing, carbonation, and processing into S-SCM, plus portland cement replacement all contribute to reducing the GWP of concrete.
Contact us today to learn more or use Solidia SCM in your ready mix.